Team:Calgary Entrepreneurial/Project/Manufacturing
From 2013.igem.org



FREDsense's website works best with Javascript enabled, especially on mobile devices. Please enable Javascript for optimal viewing.
Operations and Manufacturing
Another important aspect of our business is how we will manufacture and distribute our product. It is important to consider factors such as cost, location and timeline. Through a partnership with a local manufacturing group, we have established an operational plan that we hope can achieve our production goals at low cost.

Manufacturing
Developing Prototypes and Manufacturing Models
With a technology implementation plan in place we have developed drawings and plans to be able to optimize our prototype system and prepare it as a product for delivery into the market. Below are schematics of potential forms of our system:

While these prototypes are the primary manufacturing layouts that have been tested so far, we have also analyzed potential other means of developing prototypes such as microfluidics. An example of a microfluidic chip layout that could be used is seen below. Microfluidics offers a distinct advantage in terms of price per each unit that must be produced. Because it is on a micro-scale, it uses less of each reagent and component making them more simple to handle and effective to use. Please note, that the numbers reported on this page reflect the cuvette style cartridge.
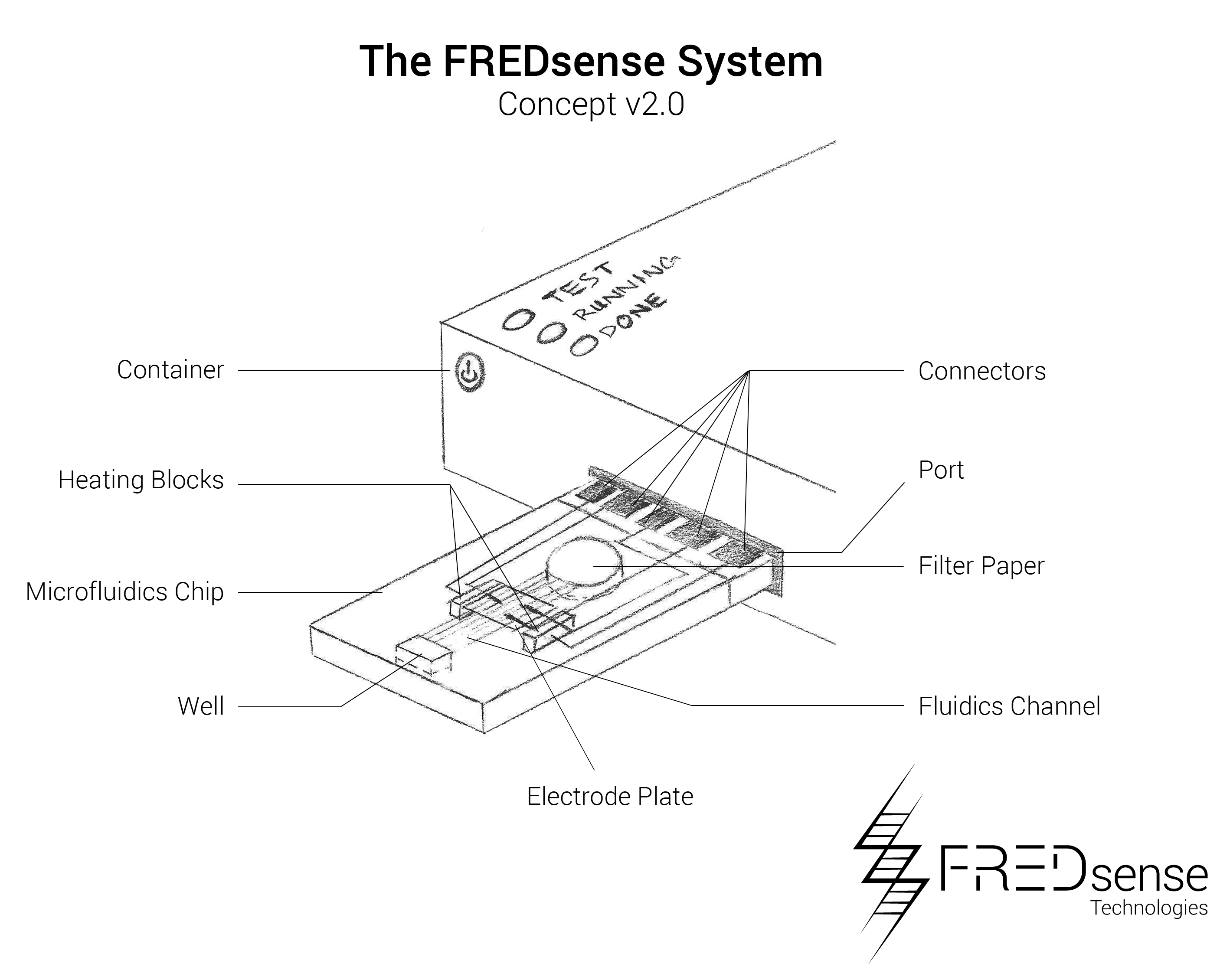
Components
These include the basic components required to build each device. The cartridge is designed to be made of a durable injectable molding plastic holding the water sample solution in a volume of approximately 1 mL giving the cuvette dimensions of about 20 mm x 50 mm x 10 mm each. A one-way valve will ensure the sample is contained within the device, and the capsule will contain a twist tube based cap which will dispense bleach once the cartridge has been finished being used. This will be used as one of our safety features of the device to ensure containment and no release of our organism into the environment
The device has a similar design made out of molded plastic that is rugged and durable to be able to be used in the field. The basic design incorporates a heat source to ensure the electrodes of the cartridges are at a consistent temperature, a potentiostat to do the electrochemical detection, and electronic systems for handling the data that is collected. The LED lights will be used as external indicators to the user if the test was successful or if it should be repeated.
Manufacturing Cost Analysis and Development Timeline
Once a lab-scale prototype has been optimized, we will move our product forward into a manufacturing development phase. To accomplish this task, we will partner with industrialization not-for-profit organizations and government programs that specialize in prototype up-scale and optimization. An overview of the cost estimations that have been made for one round of prototype development are below:
These numbers were determined by estimating the cost of each component of the project and the cost associated with batch producing 100 cartridges. To produce our final product several rounds of prototype and product development will have to be undergone to ensure the production of an effective product. It is estimated that our product development will require at least five rounds of prototype development cycles as compared to other similar products in this industry. Overall we have estimated the cost of these five rounds will be in the range of $225,000 to $275,000 depending on changes that are made to the technology through the development cycle.
Each round of prototype development will require a series of steps to design and simulate the prototype, design the molding and plastic casings for each device, assemble each component individually, and then integrate the components into the finalized system. An overview of this process and the time associated with each step is listed below:
This development plan assumes an approximate 2 month development cycle. This will require approximately one year to fully develop our final product that will be ready for mass production.
Cost of Production
Once our finalized product is ready to enter mass production, estimated analysis for the cost of building the device would require an overhead of about $215.00 per unit. Additionally, producing one of the cartridges would be equivalent to $5.80 per unit. The information for this analysis is below:
With these fixed cost of production, we would expect that in order to break-even for manufacturing, we would have to produce 260 cartridges and 18 detectors. This does not include any other over-head which will be required to produce these units. Estimating our profitability will require additional information and will be important to consider with the development of sales strategies and selling activities.
Manufacturing Operations
Production will be facilitated by partnering with key manufacturing services and operation experts. One such example of these partners would be ACAMP - the Alberta Center for the Advancement of MNT Products. This government funded organization provides expertise and funding in order to help commercialize products. The amount of manufacturing which is done by our group will be set to a minimum and only include those particular components which must be completed in a biological manufacturing facility. This will be advantageous since many of these government organizations can off-set early production costs to allow for our products to reach the market faster. In addition, this allows our company to focus on other areas of production, namely the biological components.
Creating key manufacturing partnerships will be vital in developing the technology. Our mass production strategy is summarized in the following figure:
Strategic partnership with manufacturing facility which will allow for production of a minimum of up to 10% market share value (government regulatory market detailed above) of cartridges and detector units - costs will be subsidized through government grant programs (for example Alberta Innovates Technology Futures Venture Funding) and government not-for-profit organizations focused on aiding groups to achieve manufacturing goals at limited cost.
The manufacturing facility will be responsible for design, assembly, and quality control of cartridges, specifically: plastics, electrodes, wiring, seals and bleach capsules.
The facility will also be responsible for the full design, fabrication, assembly, and quality control of the detector system: All components of the system.
Manufacturing facilities will ship cartridge components to FREDsense Technologies for addition of biological components: lyophilized bacteria and dried electroactive compounds and buffer chemicals. As these components are required in extremely low volumes (for example 100μL of bacteria per cartridge), FREDsense Technologies will have the capacity to produce these in house. As we have significant experience in growing and lyophilizing bacteria, we will also be capable of producing these components efficiently.
Shipment of cartridges to FREDsense Technologies will occur on a per-contract or sale basis depending on demand (see selling activities for details). Detectors and cartridges will be held at the FREDsense Technologies facility based on a percentage of sales from the previous three months and projections for sales in the future. This will allow for the fulfillment of small orders whereas large contracts or batch orders will take more time to distribute to the client as they will be made to order. FREDsense Technologies staff will be responsible for final assembly of the cartridges, quality control testing, packaging, and distribution for the first few years of production, until scale-up is needed. Detector systems will ideally be directly distributed from the manufacturer, however, if this is not possible, FREDsense will distribute the detectors as well. At this point, we will sub-contract to a distributor.
As capacity is reached, new manufacturing contracts will be established with larger partners and different manufacturing paradigms in order to maintain profitability and efficiency during company growth.
Assumptions - Long-term storage of the product is feasible as the bacteria and chemicals are in a lyophilized state. Bioreactor grow-up for a batch order would take 24 hours based on preliminary technical findings for our organism. We estimate that the amount of bacteria that we would potentially need for each cartridge is 0.1mL of 1x109 cells/mL, meaning that roughly a 10L bioreactor would account for over 100,000 cartridges. These numbers were determined based on the concentrations of bacteria used in our lab-scale system. Lyophilization may take up to two days which means sales turn around times may be affected for small orders. It may be of value to have a set of ready-made products that could be distributed next day.
Capacity - Starting capacity for operations will be set to accommodate the production of bulk numbers of cartridges in the hundreds (involving daily operations) with the intent of increasing this production to accommodate thousands of cartridges to be produced. This will be done through further partnerships to diverse manufacturing groups outside of Canada as we begin to move our production to a more global audience. Our first major goal in our marketing strategy is to reach 30% of the government regulation market with our product. This would require the capacity to produce approximately 15,000 cartridges per year. As the biological components for this volume of cartridges would still be small, FREDsense could feasibly produce the components necessary for this volume.
Timeframe - We plan to reach full capacity, supplying approximately 30% of the government regulation market (15,000 cartridges and 150 detectors yearly) by year three of active production as dictated in our budget and milestones section. This means we will be required to begin negotiating new contracts with larger manufacturers and distribution providers by year 2 to ensure our company continues to grow.
Manufacturing Advantages
Our technology platform provides clear manufacturing advantages compared to similar products:
Versatility - All products we hope to generate, the general toxin sensor and other second generation products, will use the same detector system. The only change in component is in the bacterial strain used in the cartridges. This provides versatile product lines to be developed with minimal additional costs in manufacturing incurred.
Multiple Strategies - Our group has identified multiple types of prototype designs to accommodate changes in cost associated with the cuvette style cartridge system (i.e. using microfluidics as an alternative to cuvettes). This will ensure that we can implement the best, most cost-effective, solution in our manufacturing.
Retaining Control - The province of Alberta has numerous government programs which allow for manufacturing contacts to be made more easily and at a discounted rate. We hope to use these types of contacts to establish relationships with key industry manufacturing players. By out-sourcing all of the non-biological components of our systems to these manufacturers, we have the ability to retain control of the sensing organism we are using while maintaining the benefits of allowing other contractors to build our detectors and partially our cartridges.