Team:Calgary Entrepreneurial/Project/Manufacturing
From 2013.igem.org



FREDsense's website works best with Javascript enabled, especially on mobile devices. Please enable Javascript for optimal viewing.
Operations and Manufacturing
Design, Optimization and Regulatory Approval
Manufacturing
Developing Prototypes and Manufacturing Models
With a technology implementation plan in place we have developed drawings and plans to be able to optimize our prototype system and prepare it as a product for delivery into the market. Below are schematics of potential forms of our system:

While these prototypes are the primary manufacturing layouts that have been tested so far, we have also analyzed potential other means of developing prototypes such as microfluidics. An example of a microfluidic chip layout that could be used is seen below. Microfluidics offers a distinct advantage in terms of price per each unit that must be produced. Because it is on a micro-scale, it uses less of each reagent and component making them more simple to handle and effective to use.
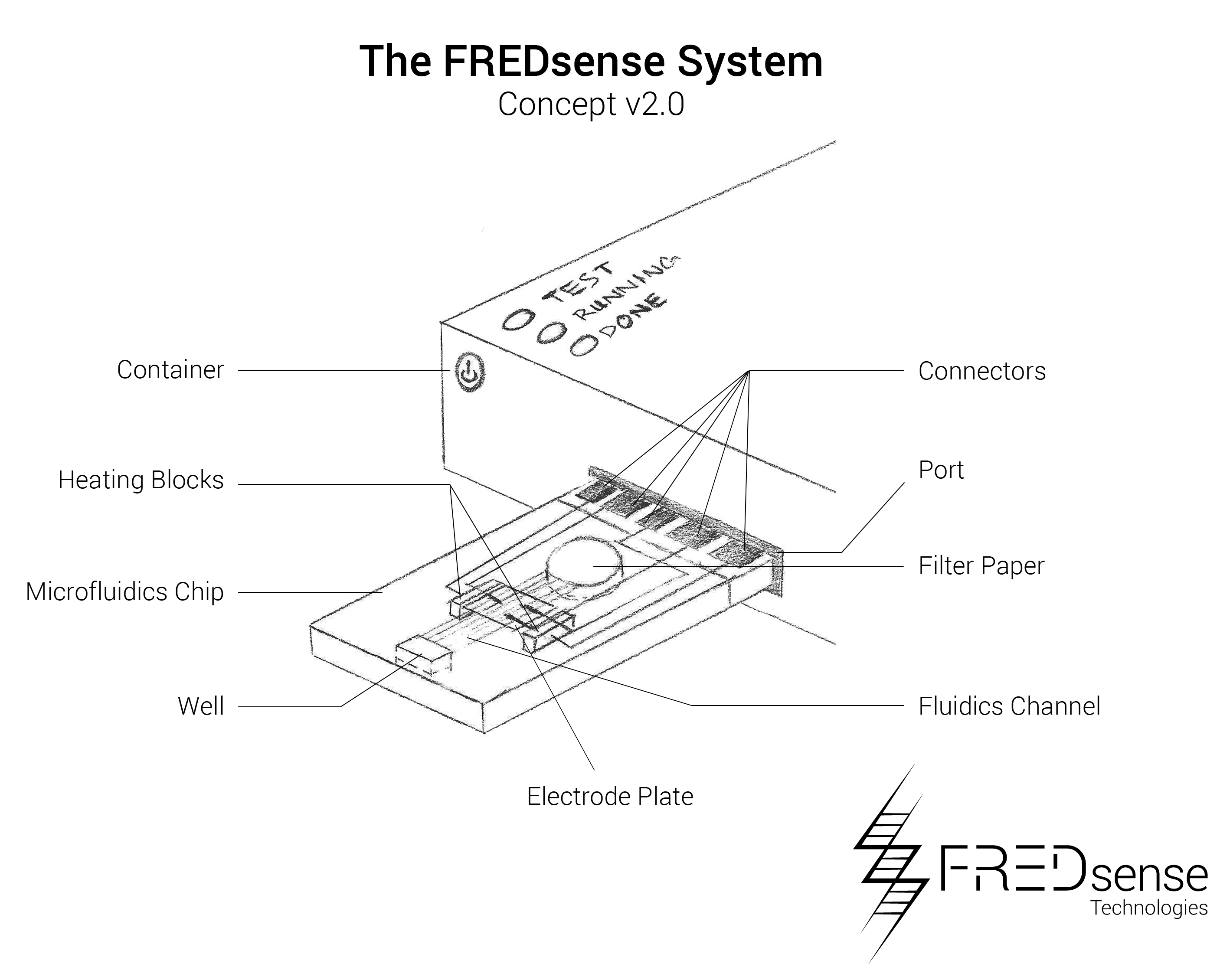
Prototype Development Timeline
Each round of prototype development will require a series of steps to design and simulate the prototype, design the molding and plastic casings for each device, assemble each component individually, and then integrate the components into the finalized system. An overview of this process and the components that would be required are shown below:
INSERT PICTURE OF GANTT LIKE CHART SHOWING TIMELINE FOR DEVELOPMENT OVERALL!!!
Cost of Production
To produce our final product several rounds of prototype and product development will have to be undergone to ensure the production of an effective product. It is estimated that our product development will require at least five rounds of prototype development cycles as compared to other similar products in this industry. Overall we have estimated the cost of these five rounds will be in the range of $200,000 to $250,000. Breakdown of this analysis is listed below:
INPUT FIGURE FROM DEVELOPMENT CYCLE COST DOCUMENT
Once our finalized product is ready to enter mass production, estimated analysis for the cost of building the device would require an overhead of about $215.00 per unit. Additionally, producing one of the catridges would be equivalent to $5.80 per unit. The information for this analysis is below:
Manufacturing Operations
Production will be facilitated by partnering with key manufacturing services and operation experts. One such example of one of these partners would be ACAMP - the Alberta Center for the Advancement of MNT Products. This government funded organization provides expertise and funding to commercialize products. These key players will be responsible for mass production of the plastics, electrical components, and hardware components for both the catridges and the final detector device. The bacterial systems will be made in-house, lyophilized, and added to the cartridge in one of our own facilities. The amount of manufacturing which is done by our group will be set to a minimum and only include those particular components which must be completed in a biological manufacturing facility.
Starting capacity for operations will be set to accomidate the production of bulk numbers of catridges in the hundreds (involving daily operations) with the intent of increasing this production to accomidate thousands of catridges to be produced. This will be done through further partnerships to diverse manufacturing groups outside of Canada as we begin to move our production to a more global audience.
I DONT KNOW WHAT TO DO FOR STANDARD COSTS OF PRODUCTION